Compresores a tornillos:
Lubricados por aceite.
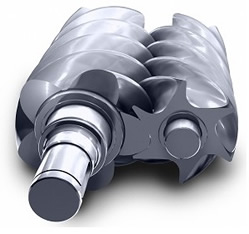
La nueva gama de compresores rotativos de tornillo con inyección de aceite de Gardner Denver incorpora los avances tecnológicos y los procesos de fabricación más vanguardistas para ofrecer a los usuarios una fuente continua de aire comprimido de alta calidad, económico y fiable.
Sistemas de aire comprimido que se adapta a todas las aplicaciones
Todo tipo de industrias, con independencia de su tamaño, confían en los compresores rotativos de tornillo Gardner Denver siempre que necesitan una fuente de aire comprimido de alta calidad. Todos los compresores de la serie se entregan con conexiones individuales de alimentación, aire comprimido y sistema de refrigeración integrado, lo que simplifica en gran medida su instalación.
Los elementos de compresión del tornillo se fabrican en la empresa utilizando la maquinaria C.N.C. más avanzada de rectificado de rotores y, a continuación, se acoplan con tecnología láser en línea para mantener las tolerancias precisas de fabricación. Como resultado, la fiabilidad y el rendimiento del compresor garantizan unos costos operativos reducidos durante toda la vida del equipo.
¿Sostenibilidad, aunque no esté limpia?
A veces, los entornos de producción industrial pueden ser sucios y polvorientos, especialmente en industrias como la ingeniería civil, la gestión de residuos, la minería y el reciclaje a cielo abierto. En este caso, los compresores lubricados por aceite no sólo funcionan de forma fiable, sino que también aumentan la rentabilidad.
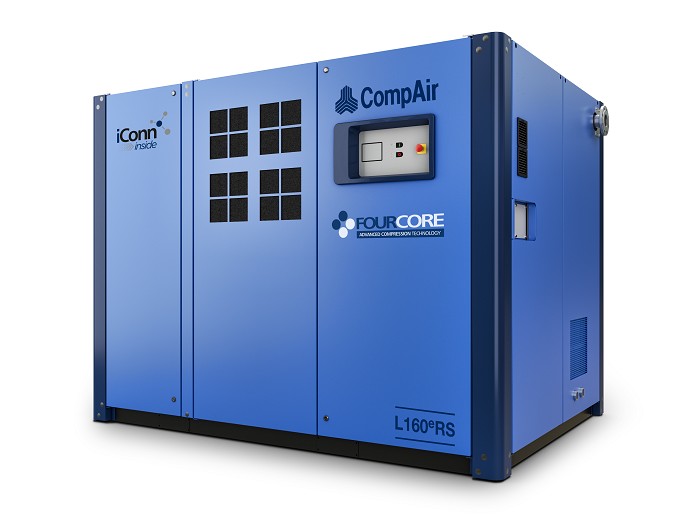
La sostenibilidad también es importante en estas industrias: con la solución de aire comprimido adecuada
El mejor ejemplo: FourCore. Con esta tecnología, usted, como empresa concientizada con el medio ambiente, puede utilizar ahora un compresor lubricado con aceite que ha sido optimizado en términos de sostenibilidad durante todo su ciclo de vida. Pero eso no es todo: FourCore ocupa el mismo espacio que una unidad de una sola etapa. Además, en comparación con los compresores convencionales de 200 kW de dos etapas, la tecnología requiere hasta un 22 % menos de material. Los consumibles se reducen en aproximadamente un 19 %.